“This program achieves SJSU’s environmental and financial goals, at the same time it works effectively on our campus where we have essentially zero storage space.”
Terri Ramirez, Recycling and Moving Services Specialist, San Jose State University
The Issue: Small Quantities of Surplus
San Jose State University (SJSU) has a student population of about 30,500 on an urban campus covering 20 square blocks. Like all big schools, SJSU generates a lot of surplus furniture and equipment. Much comes from large renovation and replacement projects. But a high proportion of SJSU’s surplus comes one or a few pieces at a time – when a professor buys a new desk, when a single classroom is refurbished, when a department renovates its office space. Over the course of the year, this small quantity surplus adds up to thousands of pieces.
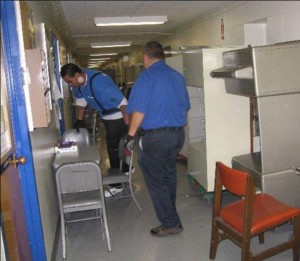
This is troublesome material. There is no room for storage on campus. The simplest thing is to toss surplus in the nearest dumpster, but most dumpsters are small 4- to 8-cubic yard boxes, unsuitable for large items like desks and chairs. There are a couple of containers for bulky items, but reaching them to discard one or a few pieces of furniture takes a lot of staff time and money. Add that cost to hauling and tip fees, and getting rid of even a small quantity of surplus is expensive.
“Getting rid” also flies in the face of SJSU’s Sustainability Policy, which places a high priority on reducing waste (SJSU’s recent reuse plus recycling rate is 91%). “Getting rid” isn’t acceptable on the SJSU campus.
That was the situation that faced Terri Ramirez, SJSU’s Recycling and Moving Services Specialist, in early 2011.
Solution: Inventory and Periodic Cleanout
Terri realized that the first step toward a solution for small-quantity surplus was to understand its quantity and composition. Collaborating first with Amy Chan and then (from 2012) with Rosario Micu, from SJSU’s Procurement Department, Terri initiated a campus-wide reporting system. Whenever staff or faculty have an item to be surplussed, they report it to the Furniture Reuse Program administrator (Rosario Micu) who maintains a running inventory of what and where it is.
Second, Terri needed a market: someone to reuse those still usable surplus items. Terri searched and found IRN. IRN matches usable surplus with a U.S and worldwide network of charities. If there’s a use for an item, IRN will find it.
Working closely together, Terri and IRN developed a straightforward solution:
- From IRN, Terri knows how much surplus she needs to fill a tractor trailer. When her inventory reaches this trip point, she calls IRN with the details: quantity, composition, description, and location.
- IRN makes a quick site visit to set up the logistics, including crew size, schedule, equipment, access and loading locations.
- IRN prepares an operations and cost proposal for the project. Depending on the quantity and location of Terri’s surplus, IRN may propose to live-load one or more trailers right on SJSU’s campus, or return the surplus to their mover’s warehouse and load trailers there.
Terri’s program was implemented in March 2011. Since then, the program has captured more than 4,300 pieces of surplus in 21 cleanouts. Before 2011, most of these items would have ended up as trash. That’s 185 tons diverted from SJSU’s waste stream, and 185 tons added to SJSU’s reuse+recycling totals.
Costs
Terri has tracked the costs of the SJSU-IRN-Suddath program, and they are less than the cost of throwing surplus away. Scheduling a crew to sweep the entire campus and load trailers is a more efficient use of manpower than sending staff to pick up and discard pieces of surplus in ones and twos. And IRN trailers packed for reuse cost much less than rolloffs filled for disposal.
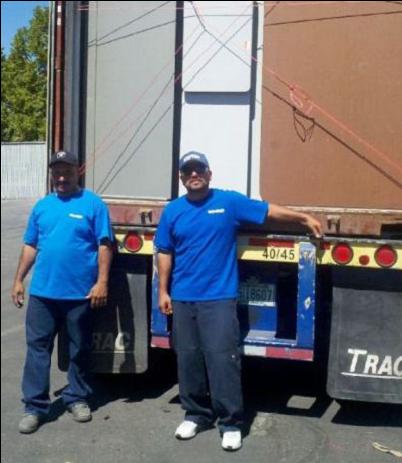
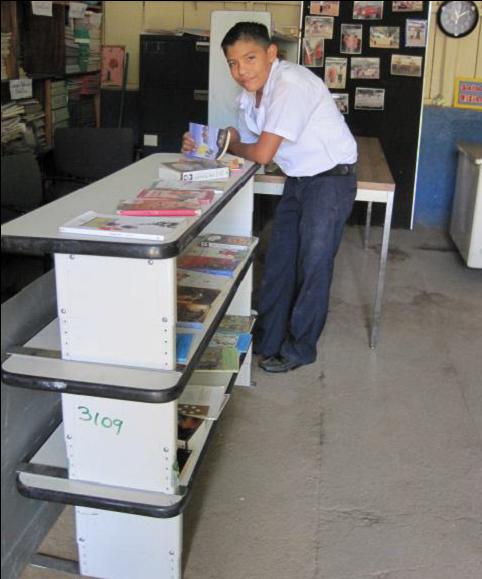