By Glenn Hasek, Green Lodging News, 5/22/2014
Glenn Hasek can be reached at editor@greenlodgingnews.com.
WILKES-BARRE, PA.—When King’s College purchased the downtown Ramada Inn in Wilkes-Barre, Pa. in late 2013, the 190-room hotel came with just about everything one would expect to come with a full-service hotel. The kitchen was fully stocked with appliances. The guestrooms still had furniture, linens, etc. Meeting rooms also still included furniture. The previous owner left just about everything for the new owner to remove—more than 4,500 items. King’s College had no intention of running a hotel; it purchased the property in order to convert it into dormitory and administrative space. King’s College could have called on a liquidator, a waste hauler, or both, but instead it called on IRN—The Recycling Network to manage the removal and placement of all unwanted items.
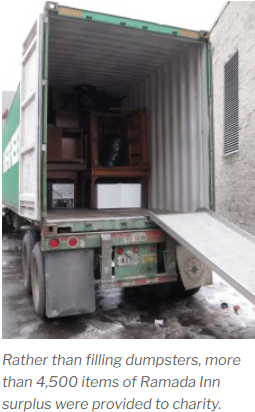
IRN, based in Concord, N.H., specializes in the recycling or placement with charities of items typically removed from hotels or other commercial spaces—paper, electronics, metals, furniture, cooking equipment and utensils, etc. IRN has even managed the recycling of pavement, roofing materials and AstroTurf. According to IRN’s Bill Yorkell, who handles sales and logistics for the organization, IRN works with more than 50 charities to place building inventory. In the case of the Ramada Inn, the inventory was matched with Salesian Missions, which is generally regarded as the largest provider of vocational and technical training in the world. Salesian Missions placed the surplus in El Salvador.
The sale of the Ramada Inn to King’s College closed on December 19, 2013. On December 20, IRN began managing the emptying of the building. IRN worked with Matheson Transfer Company, which provided a crew to remove the building’s contents. IRN’s logistics partner for the project was Intermodal Management System (IMS). IMS coordinated the arrival and departure of 17 tractor trailers over nine days.
A Highly Coordinated Packing Effort
During the project, which was completed two days ahead of schedule, Matheson divided its crew to ensure an efficient process. Half swept the guestrooms and other areas and brought the materials to a central staging area. The other half of the crew took out the staged materials and packed trailers. Specific individuals were designated to box and pad fragile items including mirrors, artwork, and lamps.
To maximize use of space in the trailers, every wardrobe and bureau drawer was filled with pillows, towels, and linens. More soft goods were used to cushion fragile items such as glassware, mirrors, and lamps. As trailers were loaded, the crew maintained a cache of small and flat items to fill small niches, and packed more small items under and around the legs of large pieces such as food prep tables. The result was a very high piece count per trailer. Ultimately, five fewer trailers were needed than first scheduled.
A total of 252 bed sets (mattresses, frames, box springs) were removed as well as about 1,000 lamps, 565 stacking chairs, 33 large kitchen appliances, 16 stainless prep tables, and many other items. According to Dana Draper, COO of IRN, what made the removal of the inventory extra challenging was having to share work space with demolition contractors who had been hired by the college. King’s College paid IRN to manage the entire process. Salesian Missions arranged and paid for the bulk of the transportation and delivery of the inventory to El Salvador.
More Than 150 Televisions Recycled
After the project was completed, it was deemed a success. In addition to the more than 4,500 items sent for reuse, about 1.7 tons was recycled as scrap metal, and more than 150 televisions weighing some 10,000 pounds were recycled. About 3.5 tons of non-usable, non-recyclable material was sent to a local disposal facility. In all, the reuse plus recycling rate for the project was 96.7 percent—a rate IRN Principal Mark Lennon says is common for IRN projects.
From a cost standpoint, working with IRN was less than sending materials to a landfill by a sizable amount, Lennon says. “We can put as much into one trailer as three or four roll-off containers,” he says. “We pack more efficiently.” Draper says the type of solution IRN provides is even more cost-effective than a liquidation/landfill approach.
The Ramada Inn project is one of about a half-dozen hotel projects on which IRN has worked. IRN works throughout the United States. According to Draper, what makes IRN unique is its ability to take on large projects. “There are organizations that are small and limited that can’t handle everything,” he says. “We are the only ones that can handle this type of volume.”
Download a PDF about this project.
Go to IRN—The Recycling Network.