Overview
A large national manufacturer asked IRN to clean out a retired manufacturing facility in eastern Massachusetts. Originally constructed in the 1930s, the plant had been used for production, storage, and administration. Production was shut down in the 1990s and administrative employees were moved out at the same time. For a number of years the plant was used for storage, but eventually this use, too, was dropped, and the plant was essentially abandoned. Left behind were a wide range of materials, including: production equipment (tanks, machinery); wood crates and pallets; off-spec plastics, adhesive powders and hardened resins; appliances; computers, monitors and other electronics; lab equipment, office furniture, racking, and other surplus; cardboard and other paper (including confidential documents); parts, piping, valves, HVAC equipment, and miscellaneous debris.
Click here for a printable PDF of this case study.
There were many challenges:
- An aged manufacturing layout with small spaces, immovable masonry walls, restrictive passageways and access points;
- Complex layout of production equipment including piping and valves;
- Large pieces of equipment erected in place;
- Hundreds of boxes and file cabinets containing production and financial records requiring handling as confidential business information;
- Complex set of materials with very different deconstruction, handling, and disposition requirements.
- Materials mixed and jumbled throughout the facility.
Planning and Implementation
IRN organized the cleanout in three phases:
Phase 1 addressed the major pieces of processing and storage equipment. These demanded specialized crews and lifting and cutting equipment. Our goal was to isolate this phase to provide a safe and orderly working environment.
Phase 2 attacked the diverse array of furnishings and supplies left over from production and administrative uses, including furniture and built-ins, boxed and filed records, computers, pallets and crates.
Phase 3 took care of “the rest” – focusing especially on recovering value from the tons of ferrous and nonferrous metal in pipes, fixtures, and wiring.
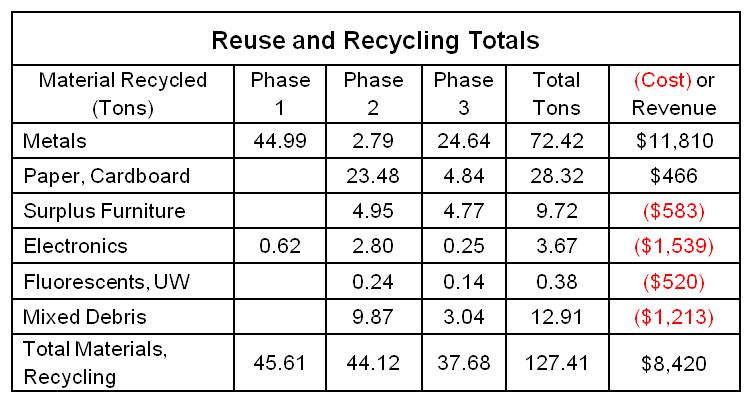
At the end of the project, zero was landfilled. About 60% of the total recovered was metal, and another 25% was paper and cardboard. All was recycled. IRN placed nearly twenty thousand pounds of excess furniture for reuse by charitable organizations. Old electronic equipment and Universal Wastes were recycled in accordance with state and federal regulations; none were disposed. The ten percent of all materials that could not be segregated for reuse or source-separated recycling were recycled as mixed debris.
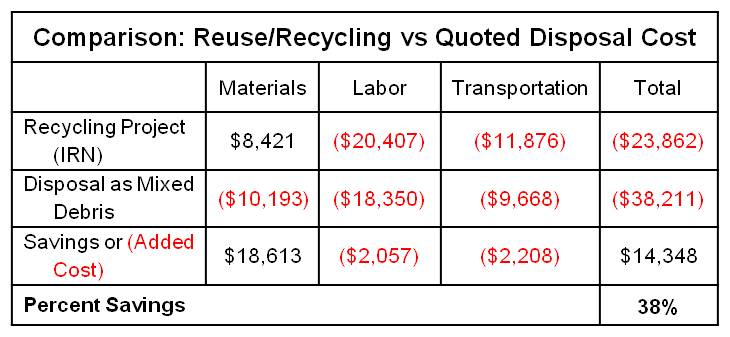
Before bringing IRN into the project, the firm had solicited prices to dispose of the “wastes” from the decommissioned facility, allowing a direct comparison with the cost of reuse and recycling. Managing for reuse+recycling added about $2,250 to labor and transportation costs, but yielded savings of more than $18,000 in the cost of material disposition. Across the entire project, reuse+ recycling yielded savings of more than $14,000, or 38% of the proposed cost to manage the project for waste disposition.
Keys to Success
Planning and Coordination. Because of the wide range of materials in the project, coupled with the fact that many items needed to be uninstalled or disassembled, careful planning and onsite coordination were required to optimize use of labor, tools, and hauling operations. Additional planning considerations related to limitations on shipping points, different crew needs for different materials and operations, and very different transportation needs for different materials.
Management and Staff Commitment. There were many barriers working in an old mill building, ranging from ancient elevators that needed to be put back into use, to snow that needed to be plowed so cranes and trucks could start work at 7:00 AM. Knowing that the project was a priority for company management, local staff jumped into the effort providing resources like extra forklifts, snow removal, and traffic control that were essential to making the project safe, efficient, and cost effective.
Communications. Effective communications with plant management, as well as communication among the many parties involved in the project, were essential to success. Just as important was communication about the financial and environmental benefits of the project. Regular updates to management and plant staff were essential to gaining employee support and their cooperation in making the project a success.